A Sustainable Story – Sonik
The development of our new double glazed door had many considerations but the key challenge was to create a sustainable glazed door which helps to limit the impact we have on the planet.
Such attention to detail drives our team, enabling it to deliver products that target function, performance and aesthetics while minimising our use of natural resources and energy.
Our designers utilised their passion for sustainability to ensure the brief was achieved. They specified locally sourced materials from the outset, mindful of the LEED v3 2009 constraints on distance travelled to site during manufacture and on deliveries of more than 500 miles.
Where possible common components and technology were used to minimise the need for new tooling and associated resources, while 3D design, simulation and rapid prototyping enabled the team to interrogate the design prior to manufacture and print new components to determine their viability. The result was the Sonik door.
Assembly instructions are printed on plastic sheets that are recovered from site to be reused. The sheets are static cling so no adhesives and cleaning agents are required. Each sheet is specific to the actual configuration of a door, rather than a generic manual that is printed and thrown away.
The dry assembly nature of the Sonik door gives it several lifecycle advantages over the equivalent bonded door. If an element such as the glass is damaged during manufacture, delivery or use, it can be replaced without also scrapping the metalwork. Since there is no bonded glass it is easy to remove the glass from the aluminium frame, which wouldn’t be the case on a similar bonded door. This also allows for easy, and therefore low energy, disassembly and separation of the constituent components for recycling, once the product is no longer in use.
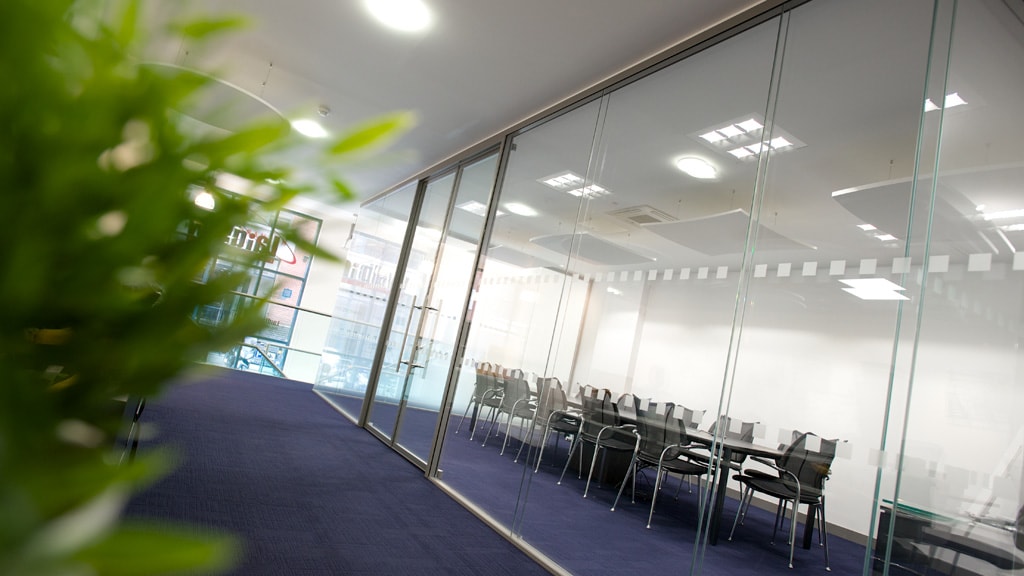
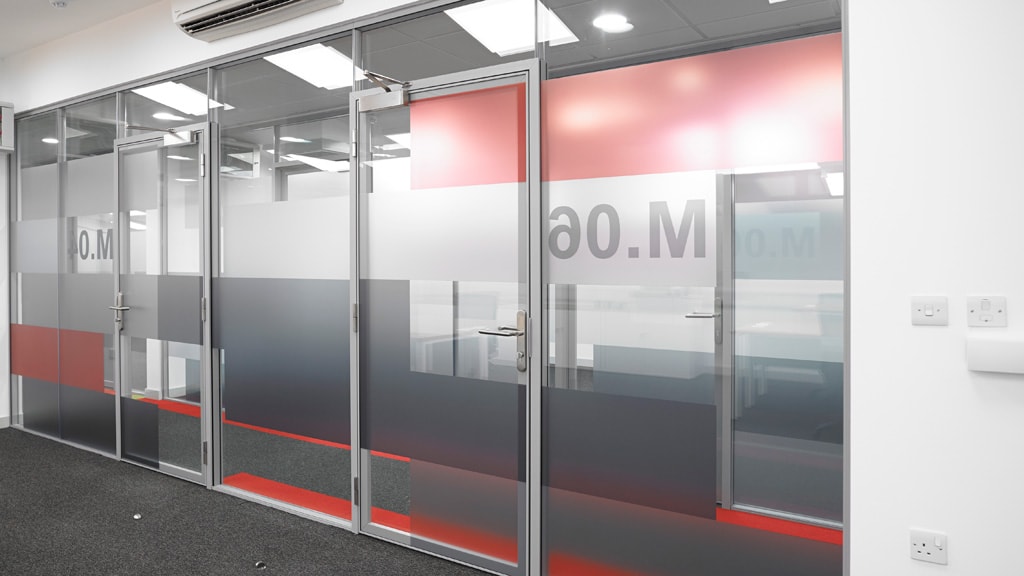